
And with recycling at the heart of Kenoteq, the business is leading the way in the adoption of a circular economy. The unique production process also allows K-Briqs to be produced in any colour, using recycled pigments in the mix.īecause of the materials used in the production of K-Briqs, they can be made anywhere, ending the need for transportation of material from further afield. Other than the obvious benefits with regards to time and environmental impact, the K-Briq also offers better insulation properties than normal bricks, keeping buildings warm in winter and cool in summer, and helping to keep energy use and heating costs down. Within 24 hours of receiving waste materials, the K-Briq is ready to use. This drastically reduces the amount of carbon released during production, and the time taken to produce the bricks.
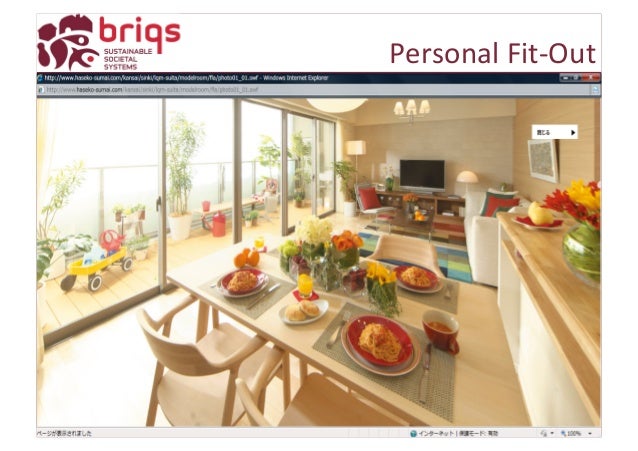
Unlike traditional bricks, there is no need to fire the K-Briq. Those recruited through briqs become members with training, development & mentorship. The recipe and process are patented in the UK and US. We started briqs to help young people to get a great first job. At the time, Briq was an internal tool that we used to give each other kudos and build team spirit. The individual BRIQs are placed on top of each other at the construction site and. The Very First Briqs It all began in 2016 at the heart of our studio. These are manufactured with high precision using robot technology from inexpensive industrial and calamity wood. The facility, which is run by Kenoteq, a start-up company set up by engineers from Heriot-Watt University, will initially manufacture 10,000 ‘K-Briqs’ a day and.
Briqs first series#
Once collected and sorted, the materials go through a series of compression and mixing processes. Our TRIQBRIQ timber construction system consists of micro-modular timber building blocks the so-called BRIQs. The first commercial production line for an eco-friendly brick with around one tenth the carbon footprint of a regular brick is due to start operation in Scotland later this year.
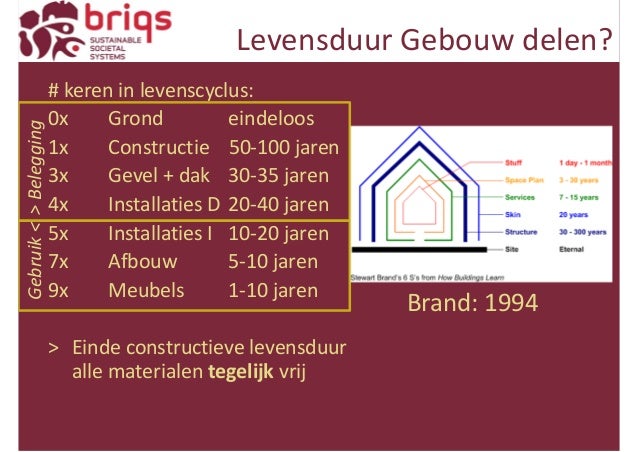
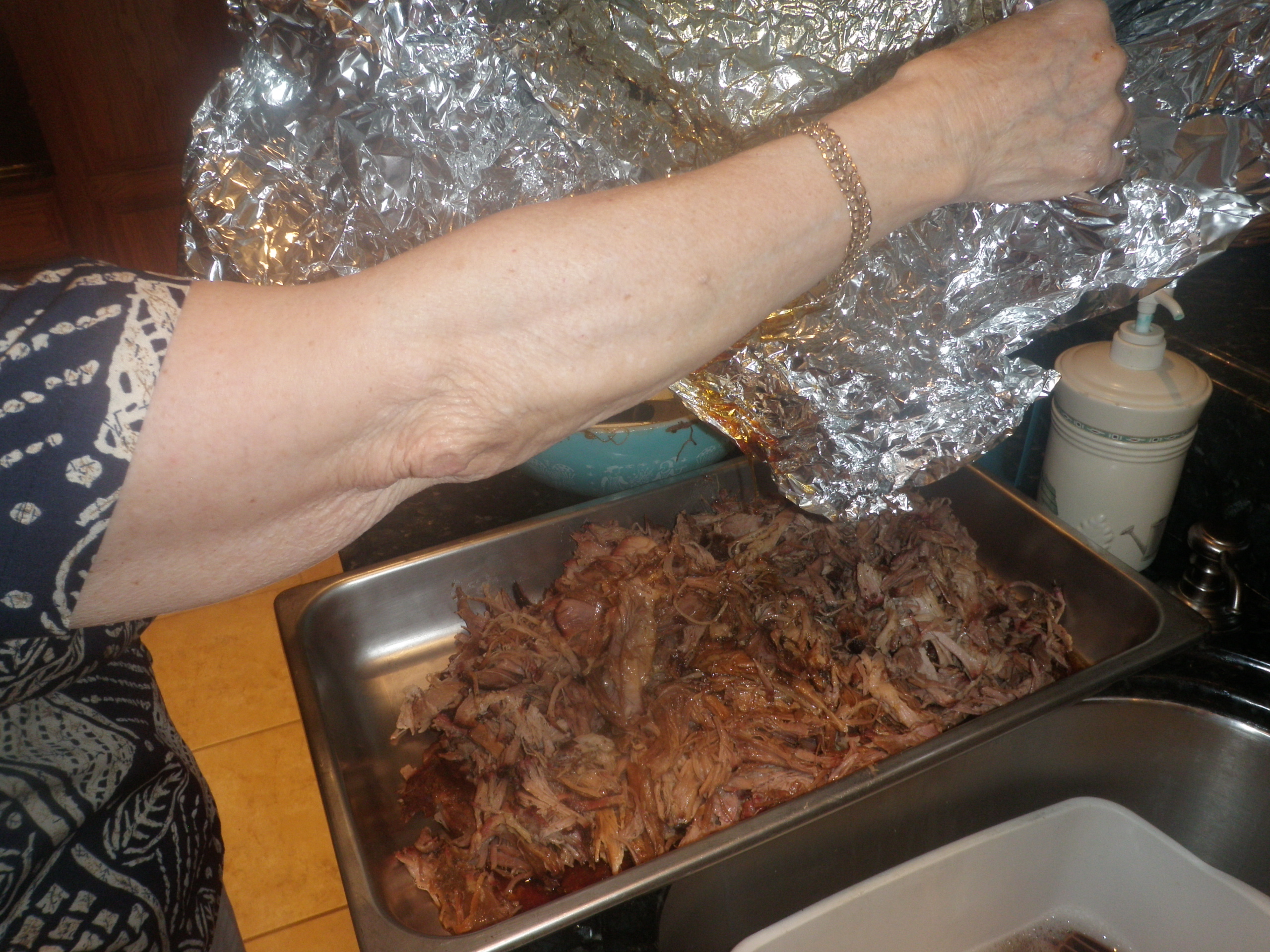
This can include high quality, recycled sands and gravels, gypsum from waste plasterboard, and recycled pigments. No sector specific skills or knowledge are required for. The process for producing a K-Briq begins with demolition or construction waste. Catch22 is recruiting for a Development Coordinator to play a key role in the Catch22 Development team. The K-Briq, made almost entirely of recycled building material, is leading the move to cleaner and more efficient building solutions.ĭesigned and developed by Professor Gabriela Medero and Dr Samuel Chapman of Edinburgh’s Heriot-Watt University over a period of years, the K-Briq went through a series of rigorous experiments and tests, and the result is a brick made from 90% recycled building material, that produces less than a tenth of the carbon emissions in its manufacture than a traditional brick. Located in Wausau Merrill Ave. With the construction industry one of the leading contributors of CO 2, a new product from start-up Kenoteq is changing the game.
